Geschichte der Jute: Garnherstellung
TEIL 4/5
Sobald die Chargenverarbeitung (Batching) der Rohjute abgeschlossen ist und die Jute ruhen konnte, ist sie für die nächsten Verarbeitungsschritte der Garnherstellung bereit – Kardieren, Verstrecken und Spinnen.
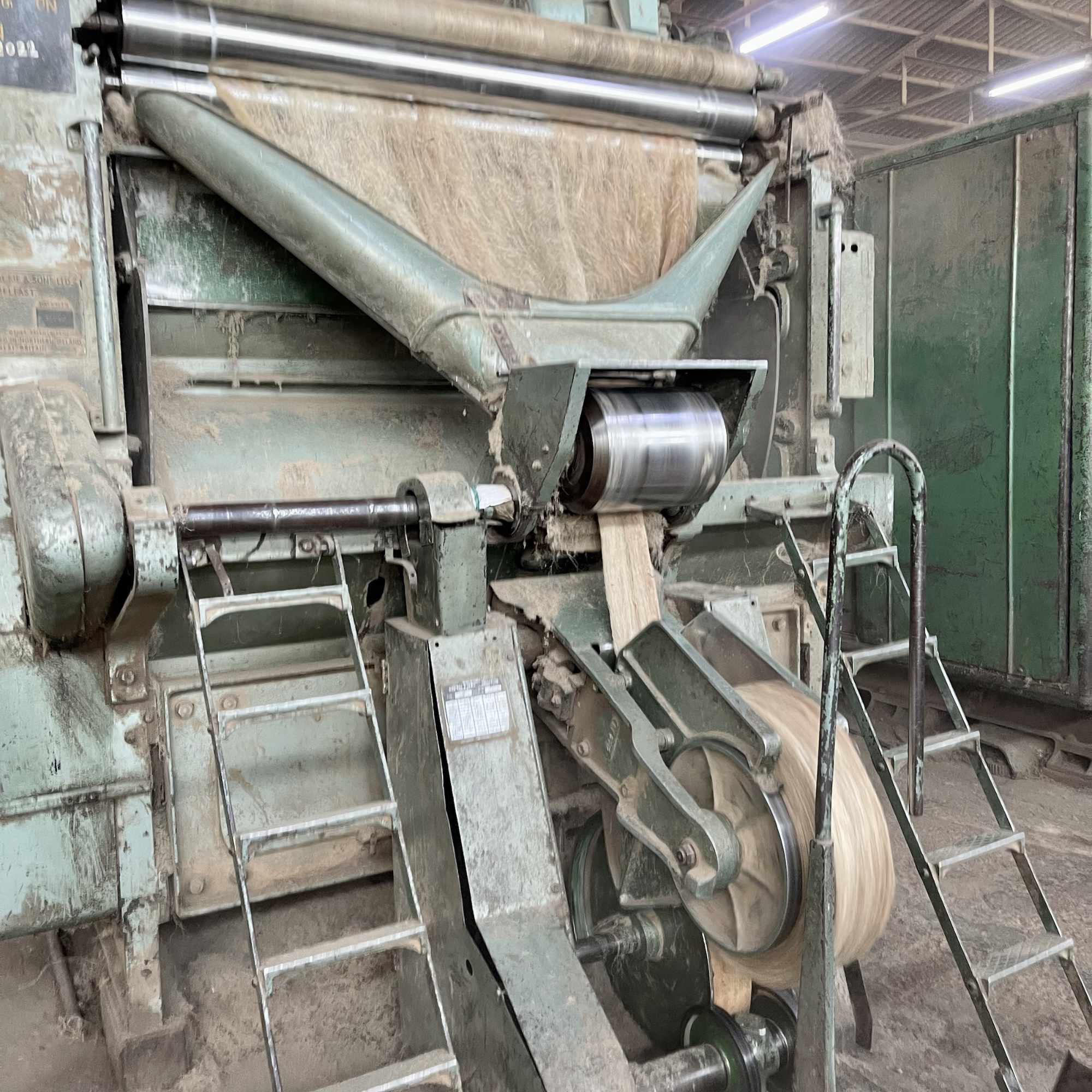
In der Garnfabrik, welche das Garn für unsere Jouyoku-Seilprodukte liefert, ist die Lagerzeit der Jutefaser zu Ende und die dicke Abdeckung aus Sackleinen wird entfernt. Die Lagerzeit ist erforderlich, um die Jutefaser für das Spinnen zum Garn weich zu machen. Selbst in der sowieso schon 38°C heißen Umgebung mit 90+% Luftfeuchtigkeit, spüre ich die Hitze, die von der gelagerten Jute ausgeht, deutlich. Die noch feuchten Juterollen ø1,2m x 40cm werden aus den Stahlringen entnommen und auf die erste Stufe der Kardiermaschine geladen. Bevor die Maschine startete, berührte ich die Außenseite der Rolle mit meiner Hand und konnte die davon ausgehende Wärme von 45-50°C deutlich spüren.
Das Band aus gewickelten Jutefilamenten läuft in die erste Stufe der Kardiermaschine, die nun damit beginnt die Filamente parallel zu kämmen. Am oberen Ende werden die Filamente weit ausgebreitet und durchlaufen mehrere Edelstahlwalzen, bevor sie auf eine andere Rolle zurückgewickelt werden. Mit Hilfe eines Übersetzers haben wir den Kardierungsleiter gebeten uns den Prozess zu erklären. Er behauptet, dass er aufgrund seiner Erfahrung und seines Fachwissens durch das bloße Betrachten einer Rolle sofort sagen kann, wie viele Phasen sie durchlaufen hat.
Sobald das Kardieren der ersten Stufe abgeschlossen und die resultierende Rolle voll ist, wird diese zwei Meter zur nächsten Maschine transportiert, um auf die Kardiermaschine der zweiten Stufe geladen zu werden. Uns wird erklärt, dass es in großen Garnfabriken, die Garne für minderwertige Anwendungen herstellen, üblich ist, nur zwei oder drei Kardierstufen zu haben, um Zeit und Kosten zu sparen. Hier gab es vier, und dies, zusammen mit hochwertiger Rohjute, höherem Dosiervolumen, kürzerer Stapelung bei höherer Temperatur, Verstreckung und Endbeschichtung. All dies wirkt sich auf die endgültige Garnweichheit, Festigkeit, Haarigkeit und den Faserverlust aus.
Nachdem der 4-stufige Kardierprozess abgeschlossen ist, wird die parallel gekämmte Rolle auf die erste Stufe des Verstreckungssystems geladen. Bei der Verstreckung wird die optimale Filamentüberlappung für die maximal erreichbare Festigkeit des fertigen Garns angestrebt. Wir wurden darüber informiert, dass die meisten Garnfabriken nur eine einzige Verstreckungsstufe haben, um Produktionskosten zu minimieren. Hier sind vier Maschinen zur Verstreckung im Einsatz, um eine verbesserte durchschnittliche Festigkeit zu erzielen.
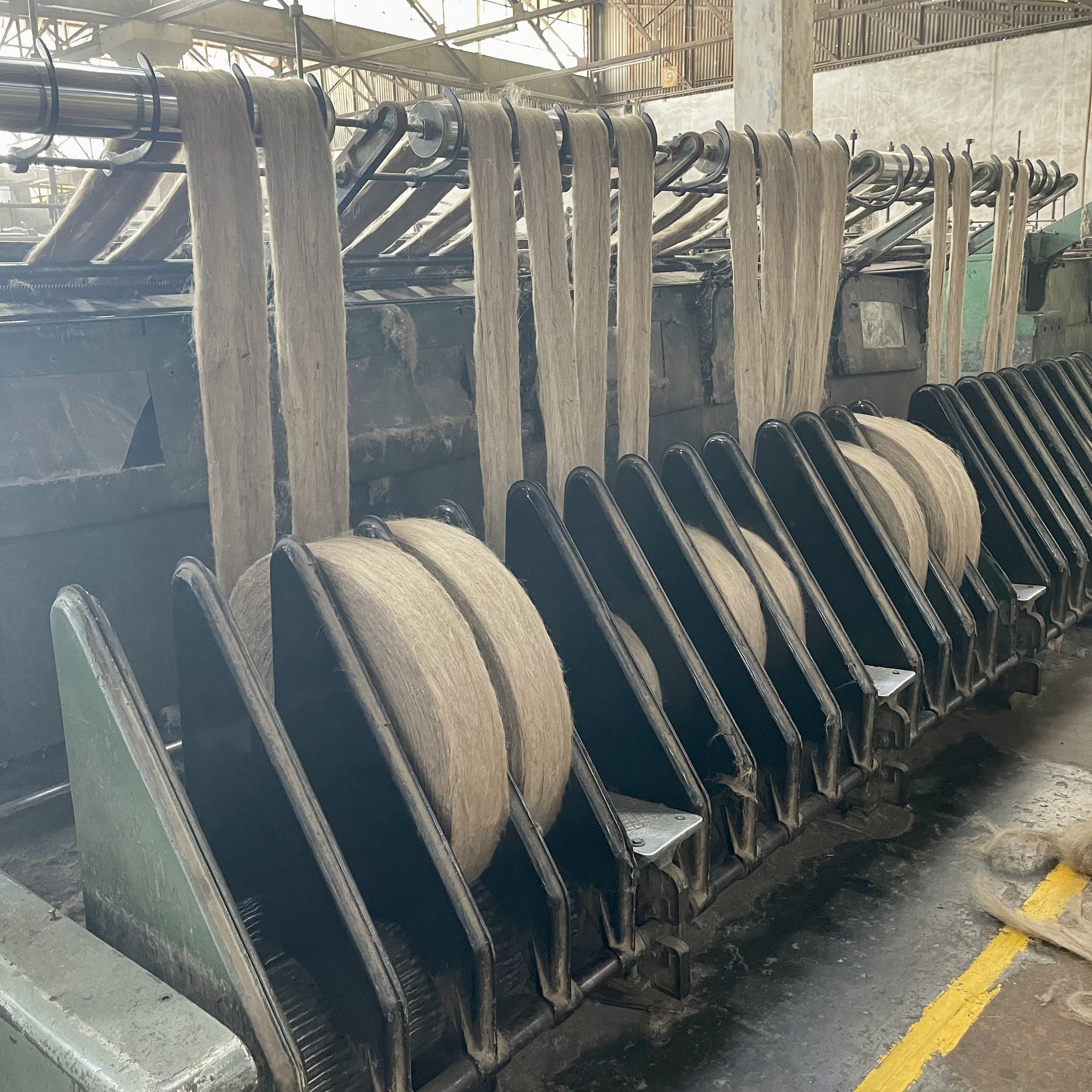

Jede Verstreckungsstufe erzeugt einen Streifen - ein riemenartiges Band aus Jutefasern, das in ein großes Fass hineingeschoben und mit einem sich auf- und abbewegenden vertikalen Metallkolben nach unten gedrückt wird. Es gibt Dutzende davon in dieser Anlage. Während die erste Verstreckungsmaschine so konzipiert ist, dass sie von einer Kardierrolle eingespeist wird, nehmen weitere Verstreckungssysteme zunehmend verstreckte Bänder aus den Fässern auf. Die Einstellung der letzten Verstreckungsmaschine bestimmt die endgültige Bandbreite. Die Bandbreite wiederrum bestimmt in der erste Spinnstufe das Garngewicht (Jute Count) - das Gewicht in britischen imperialen Pfund pro 14.400 Yards. In allen Garnfabriken beginnt dieser Prozessabschnitt mit einem einlagigen Garn.
Garnknoten in Juteseilen sind ungern gesehen. Da die Spulengröße der ersten einlagigen Spinnstufe jedoch begrenzt ist, können Knoten leider nie komplett beseitigt werden. Würde man die Länge der Bänder, die aus der Verstreckungsstufe eingespeist und zu Garn verdreht werden, erhöhen, so würde dies die Spinneffizienz der Maschinentechnik beeinträchtigen, da sich das Gewicht erhöht und die Maschinentechnik nicht in der Lage ist, mit schweren Lasten umzugehen. Es wird uns erklärt, dass aufgrund der diffizilen Natur dieser Phase die Maschineneinstellungen für ankommende zerkleinerte, sortierte, gestapelte, kardierte und verstreckte Jute so optimiert werden müssen, dass Brüche im Garn vermieden werden. Jedes Spinnsystem hat eine Vielzahl von Wickelspulen. Sollte es zu einem (Garn-)Bruch an einer Spule kommen würde das zu sehr ernsten Produktionsausfällen führen.
Sobald die Spinnspulen mit Garn beladen sind, werden sie entweder direkt zur Garnspulenwicklung für kundenspezifische Auftrag weitergegeben oder anderen Prozessen zugewiesen. Spinnspulen werden immer zusammen mit den Spulenkernen, welche für die entsprechenden Web- oder Zwirnmaschinen erforderlich sind, weitergegeben, deshalb ist es notwendig, dass kleine Spinnmaschinenspulen mit Garn mit einem unvermeidlichen Knoten verbunden werden.
Für unsere Anwendung gibt es eine proprietäre mechanische Zwischenstufe, die unser Garn verdichtet, um den Faserverlust und die Haarigkeit deutlich zu reduzieren. Für andere Kunden kann das Garn z.B. mehrlagig verdreht werden, wie zum Verschnüren von (Heu-)Ballen oder zu Zwirn. Uns wird ein Beispiel für das leichteste einlagige Garn (7lb), bis hin zu 4-lagige 80lb-Schnur (4 x 20lb) gezeigt. Mehrlagige Garne, so wird uns gesagt, sind nicht für die Verarbeitung zu Seilen bestimmt.
Uns wurden Mehrlagen-Zwirnmaschinen gezeigt und die Dynamik erklärt. Es sind 3 Drehdynamiken erforderlich. In einem Seil oder einer Schnur ist die erste Verdrehung die des einlagigen Garns, in unserem, und fast allen Fällen, aufgrund der verfügbaren Maschinen eine "Z-Schlagung" oder „rechtsdrehend“, wenn Sie am Garn hinunterschauen. Dem wird dann durch eine entsprechende umgekehrte Verdrehung entgegengewirkt, wenn die Garne zu einem Strang verdreht werden. Und schließlich folgt, entgegen den zwei vorherigen Dynamiken, in der ursprünglichen Garnrichtung, die Verdrehung der Stränge zu einem Seil.
Bei einem Erntegarn oder einer Bindeschnur besteht die zweite Dynamik in der Gegenverdrehung, bei der mehrere Garnen zusammengefasst werden. Wird das Endprodukt schließlich verdreht, hat es die endgültige Dynamik erzielt. Das Hinzufügen einer vierten Dynamik, um Zwirne oder Schnur zu einem Seil zu verdrehen, wird daher als unlogisch betrachtet.
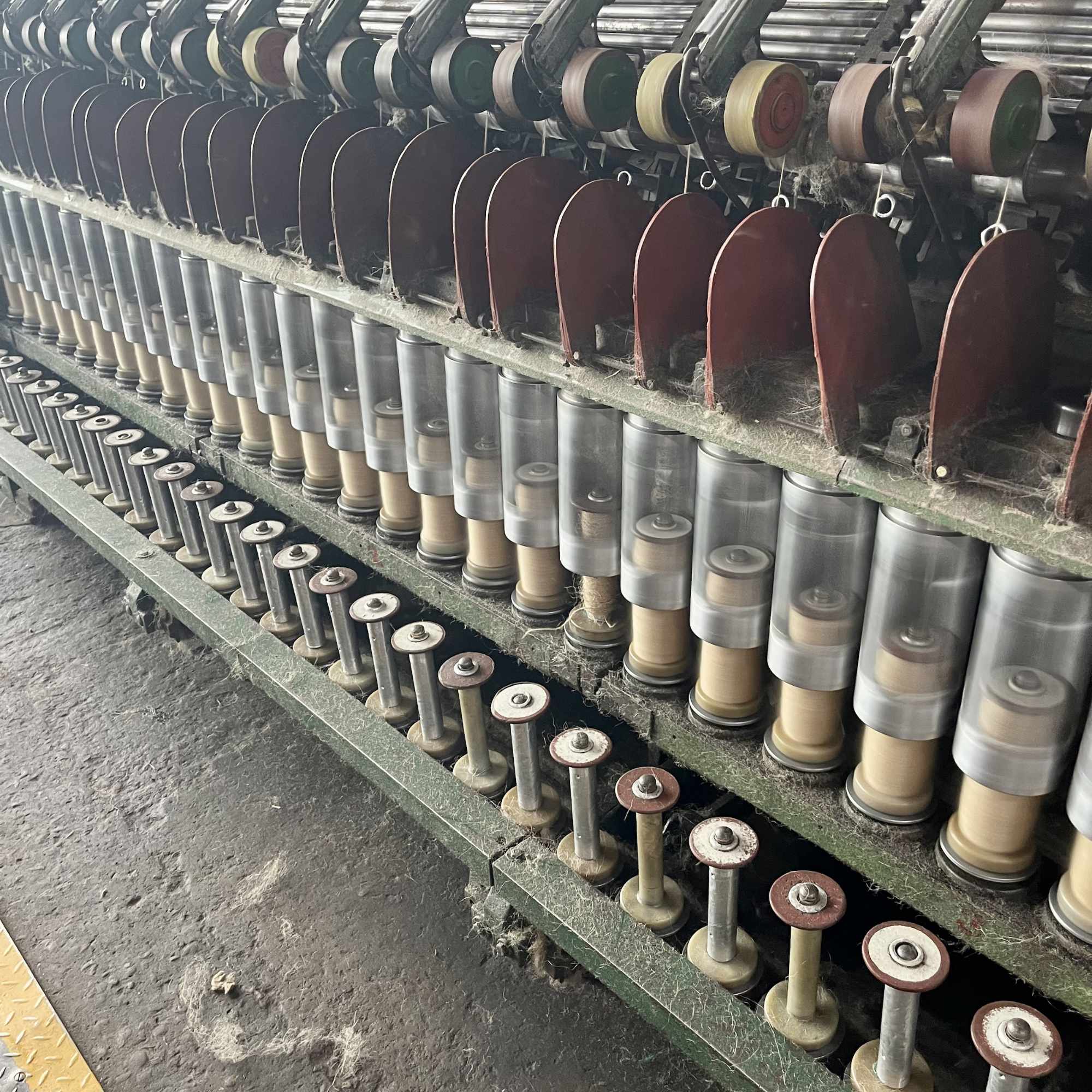
Die letzte notwendige Prozessstufe ist die Beschichtung, bei welcher der Flüssigkeitskontakt gefolgt von einer Infrarottrocknung dazu beiträgt, den Verlust von Haaren und Fasern weiter zu verhindern. Wir sollten jedoch realistisch sein und verstehen, dass Jute bis zu einem gewissen Grad immer von Natur aus haarig ist und dass der anfängliche Abrieb beim Gebrauch zu einer gewissen Entfernung der Beschichtung und zur Förderung des Haaraustritts führt. Dieser Haaraustritt wird mit erhöhter Verwendung und menschlicher Hautölbeschichtung poliert und teilweise entfernt, kann aber auch durch eine manuelle Beschichtung von Hand mit Öl vor dem Gebrauch verringert werden, z. B. Jojoba oder Tsubaki usw.
Die Kunden dieser Garnfabrik benötigen eine Vielzahl von Garnspulenspezifikationen, die passend zu ihren jeweiligen Maschinen geliefert werden müssen. Wir sehen parallele, konische, hohe und große Garnspulen von 3 bis 20 kg im Versandbereich, wo Ware bis zu 6m Höhe gestapelt wird.
Zurück bei der
letzten Reihe der Garnspulenwickelsysteme betrachten wir die Garne der kleineren
Spinnsystemspulen mit Knoten verbunden werden. Gelegentlich kann eine
Verunreinigung eine Schwachstelle sein, so dass das Garn bricht und wieder
verbunden werden muss. Nachdem wir bisher nur gewöhnliche einfache Riffknoten
gesehen haben, die zum Verbinden von Garnen verwendet werden, wird uns hier ein
einzigartiger geheimer Knoten gezeigt, der nur in dieser speziellen Garnfabrik
verwendet wird und deutlich besser verdichtet. Die abstehenden Enden werden
sorgfältig auf <3 mm getrimmt.
©AMATSUNAWA GmbH 2022