Die Geschichte der Jute: Chargenverarbeitung (Batching)
TEIL 3 / 5
Von den Anbaustandorten wird die Rohjute zur Verarbeitung in die Garnfabriken gebraucht. Die Verarbeitung beginnt mit dem Zerkleinern, dem Gradieren, der Chargenverarbeitung und dem Stapeln.
Auf bunt bemalten Lastwagen, für die ein Mad Max-Filmregisseur sein letztes Hemd geben würde, treffen die Morah-Ballen aus Rohjute in den Garnfabriken ein. Viele der LKWs sind schon seit Jahrzehnten im Einsatz und ich entdecke unter der Vielzahl einige britische Oldtimer und indische TATA-Modelle. Die Fahrer stapeln ihre Ladungen auf eine Art und Weise, die unsere westliche Verkehrspolizei dazu veranlassen würde, das Fahrzeug umgehend anzuhalten, um die Waren fest unter einer Plane zu verzurren.
Es war nicht einfach unsere Garnfabrik zu finden. Das Durcheinander aus Bangla Bornomala-Schrift ist für mich unmöglich zu lesen. Als wir Fußgänger aus dem Fenster nach dem Weg fragten, hatten wir den unscheinbaren Eingang lediglich um ein paar hundert Meter verpasst. Nach gewohnter Art und Weise machte unser Fahrer eine Kehrtwende auf unsere Straßenseite der 3-spurigen Autobahn, die durch einen Mittelplanke aus Beton von der anderen Fahrspur getrennt war. Entgegen dem Verkehrsfluss fuhren wir zurück. Unser Fahrer hupte den ganze Fahrtabschnitt über, um entgegenkommende Fahrzeuge vor uns zu warnen.

Unsere Garnfabrik beschäftigt 2.700 Mitarbeiter auf einem 12 Hektar großen Gelände und produziert etwa 100 Tonnen Garn pro Tag, 365 Tage im Jahr in einem 24/7 3-Schicht-Betrieb. Es wird nur 100% Tosha-Jute einkauft, nicht die typische Mischung mit minderwertiger Meshta-Faser. Alle Produkte hier sind für qualitativ hochwertige Anwendungen vorgesehen. Nachdem wir das Team getroffen haben, erklärten der Vorsitzende und der Vizepräsident bei Tee und Kuchen die Geschichte und den Betrieb des Unternehmens, bevor wir aus dem klimatisierten Sitzungssaal zu einer Tour bei hoher Luftfeuchtigkeit aufbrachen.
Der erste Halt ist die Anlegestelle am Shitalakshya-Fluss, einem Nebenfluss des Brahmaputra. Hier kommt die Rohjute auf einem Frachtkahn an. Dann geht es weiter und zu und in den riesigen Lagerschuppen für ankommende Morah-Ballen. Tausende Tonnen Ballen aus Rohjute, alle gefaltet und gestapelt, selbst noch am Ende der 2021er Saison. Was mir sofort auffiel, war das Nichtvorhandensein von Jutestaub. Der Vorsitzende erklärte mir, dass sich der Staub mit der Verarbeitung von minderwertigem Material in den größeren Fabriken, die Garne für Low-End-Anwendungen herstellen, wie z.B. Sackleinen, mittelschwere und schwere Hessian-Tücher und Teppichrücken, zunehmend verschlimmert.
Wir durchquerten einen Bereich, indem mehrere Arbeiter über einem Rechteck aus gemein aussehender Metallspieße, die auf einer Metallplatte montiert waren, Filamente zerkleinerten. Die „Hackler“ (Zerkleinerer) öffnen die Morah-Ballen und schneiden das Wurzelende mit einer Machete auf einem hölzernen Baumstumpfblock ab, da dies die meisten Verunreinigungen enthält. Die Wurzelabfälle werden an andere Spinnereien verkauft und für qualitativ-minderwertigere Garne verwendet. Jeder trägt Gesichtsmasken, nicht wegen dem Staub, sondern aufgrund der aktuell strengen COVID-Richtlinie des Betriebs.
Die Filamente werden dann mehrmals von Hand über die Metallspitzen geschlagen, um verbleibende kleinere Verunreinigungen zu entfernen. Dies geschieht so lange, bis die allermeisten abgefallen sind. Wie bei jedem anderen landwirtschaftlichen Material auch, wäre es falsch zu erwarten, dass alle Verunreinigungen entfernt werden können, zumindest nicht ohne einschneidende technische Fortschritte und Mechanisierung. In meinem Kopf träumte ich von Bildverarbeitung und Laserscanning. Dies würde den Preis für das Produkt jedoch astronomisch in die Höhe treiben.
Während das Zerkleinern weiterging, wurden die Metallspitzen und Blöcke näher an die nächste Reihe gestapelter Morah-Ballen herangerückt. Das zerkleinerte Material wurde nach Qualität sortiert („gegraded“) und auf Karren verladen. Von hier aus wird die Jute je nach Qualitätsstufe für verschiedene Garne in die Halle zur Chargenverarbeitung („batching“) geschleppt.
In der Halle der Chargenverarbeitung war ich überrascht von dem leicht süßlichen Geruch. Da diese Mühle nur regional produziertes, hochwertiges, nicht ranzig-werdendes und mit 100% Vitamin A und D angereichertes kaltgepresstes Sojabohnenöl verwendet, gibt es keinen Gestank, der mit weißem Mineralöl (JBO) in Verbindung gebracht werden konnte. Der Vorsitzende wies erneut darauf hin, dass die Dämpfe in den größeren Garnfabriken, welche JBO verwenden, unerträglich sein können. Ganz offensichtlich, war ich mehr als nur erfreut darüber, da ich nun wusste, dass hier keine Kontamination mit JBO möglich war.
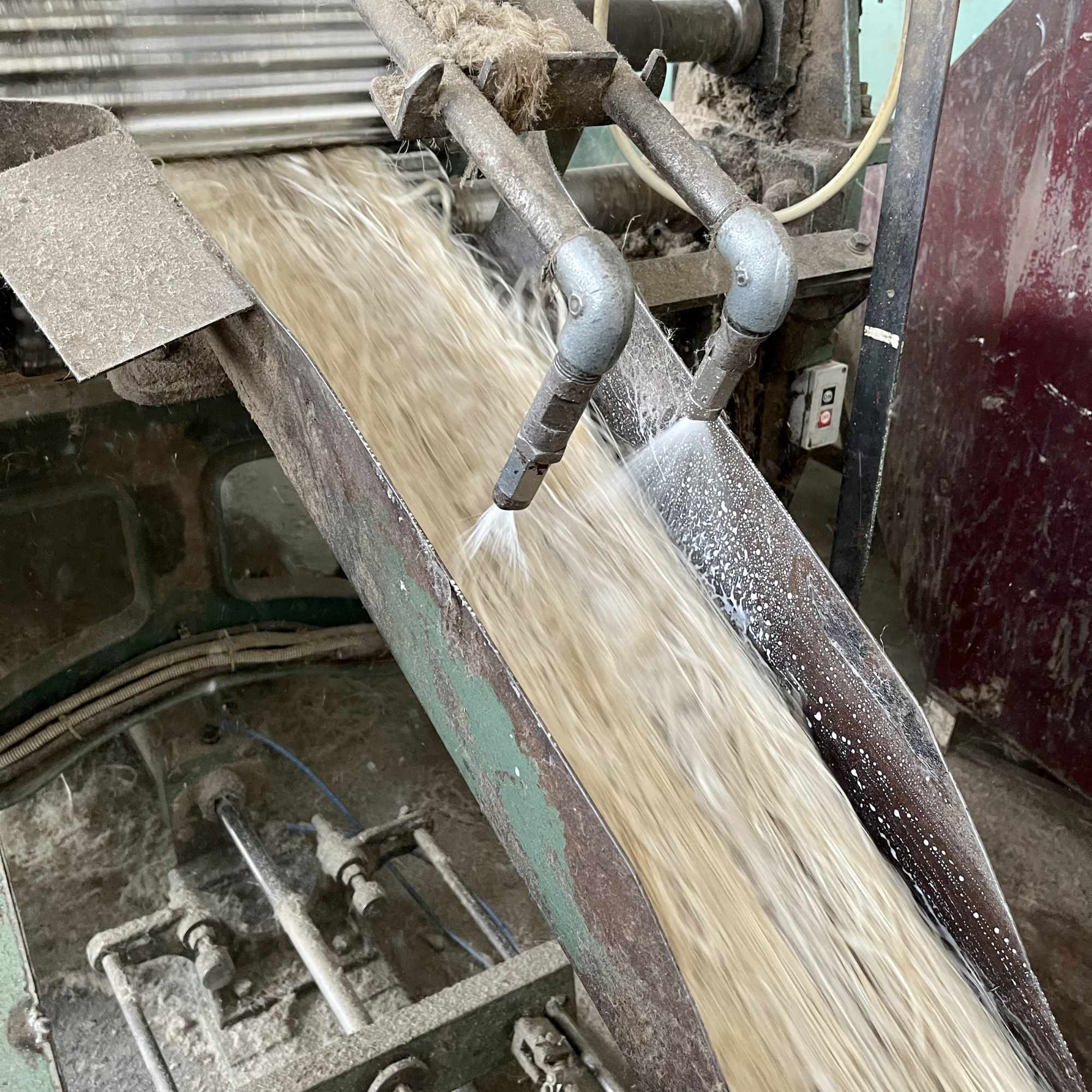
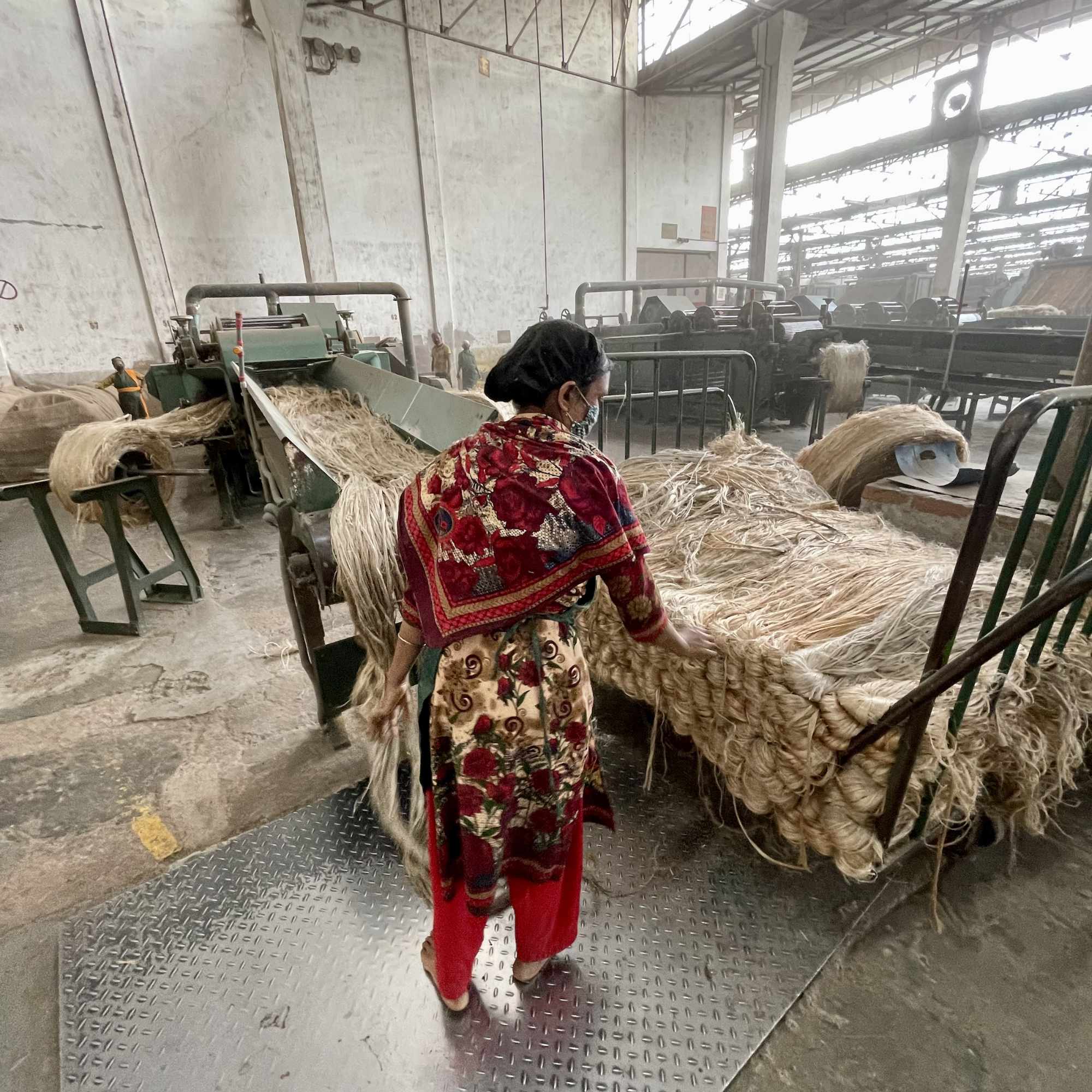
Die Filamente werden vom Karren genommen, aufgefaltet und von einer barfüßigen Dame längs auf das Chargensystem gelegt, wo diese durch eine Reihe von Walzen transportiert werden, um einen „Faserfluss“ von 40cm Breite zu erzeugen. Am Ende gibt es 2 Sprühköpfe, einen für Wasser und einen für Öl. In dieser Garnfabrik wird kein Emulgator verwendet.
Das erzeugte Band aus nasser Jute wird von der Maschine zu einer Rolle mit einem Durchmesser von ca. 1,2m Meter aufgerollt. Wenn die Rolle voll ist, wird diese wieder in die Maschine eingesetzt und seitlich in das System eingespeist, so dass sie mit weiterer Roh-Jute vermischt wird. Dieser Vorgang wird mehrmals wiederholt, um eine gute Penetration zu erzielen. Wenn eine Rolle vollständig „gebatched“ ist, wird diese in einen Stahlring eingelegt und mit dessen Hilfe zum Stapelplatz gerollt. Hier wird sie nun mit dickem Sackleinen aus Jute abgedeckt, damit die Wärme nicht entweichen kann.
Jede Garnspinnerei entwickelt ihre eigenen Techniken, um Garne speziell für ihr Einzugsgebiet herzustellen. JBO-Jute wird gewöhnlich für 48 Stunden gestapelt. Diese Zeit ist ausreichend, um die Fasern für die nachfolgenden Verarbeitungsstufen aufzuweichen. Jutefasern, die mit Pflanzenölen "gebatched" werden, benötigen mehr als eine Woche, um den notwendigen Grad an Weichheit zu erreichen. Dies ist auch abhängig vom verwendeten Öl, das Palmöl, Rizinusöl, Reiskeimöl oder Sojabohnenöl sein kann. Mir wurde erklärt, dass die mehrstufige Chargenverabeitung mit höheren, hochwertigeren Dosiervolumen und das Lagern in den Stahlringen unter dickem Sackleinen die Temperatur im Stapel beschleunigt und die Lagerdauer auf 72 bis 84 Stunden reduziert.
©AMATSUNAWA GmbH 2022
