Jute Batching
The process to soften jute filaments for yarn production.
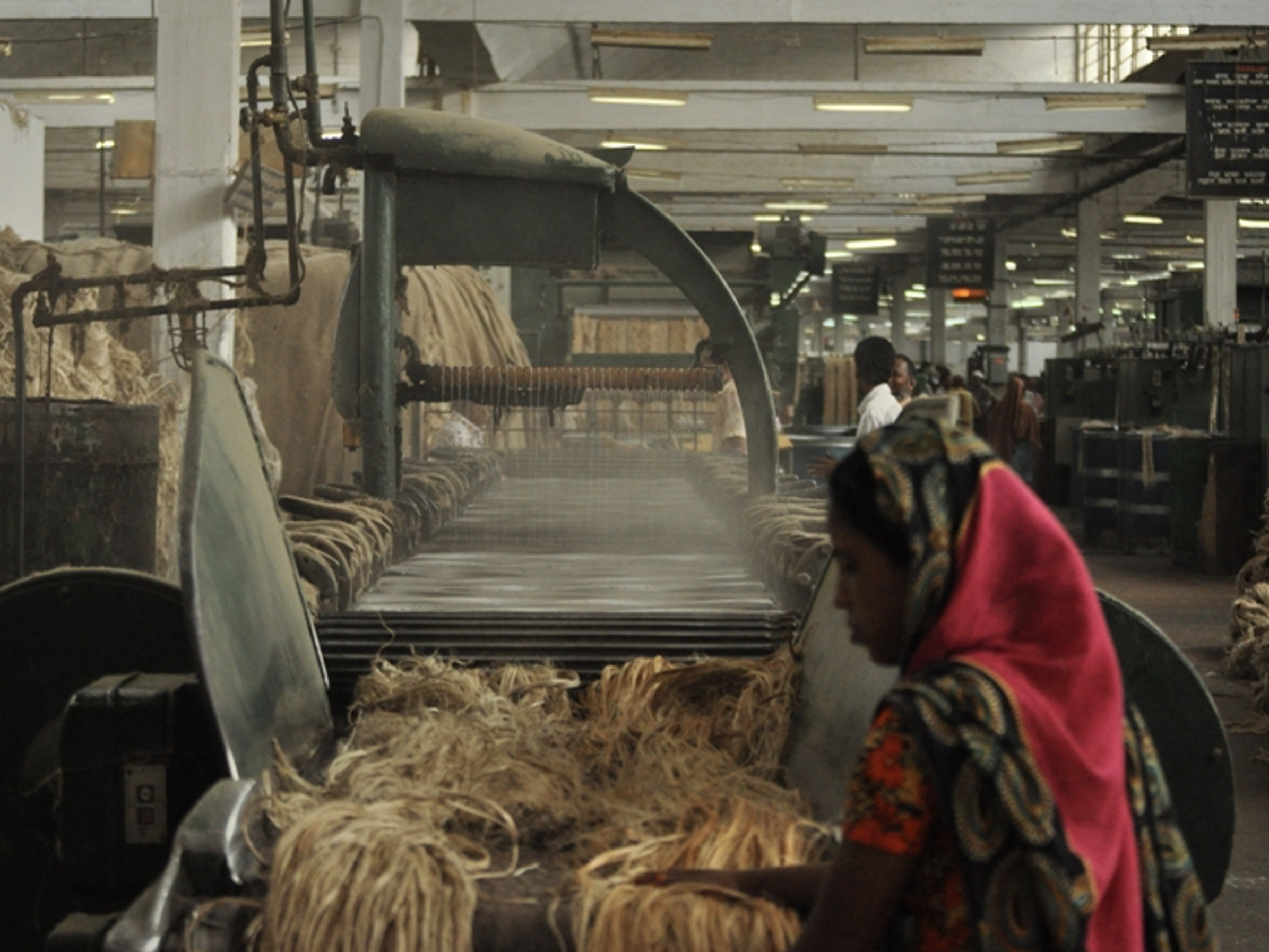
Information on jute batching
On arrival at the mill, manual hackling segregation sorts the longest, strongest filaments down through decreasing quality until only dust remains.
The next process is batching, invented in 1833 by Thomas Neigh in Dundee, Scotland using whale oil, and used to soften wiry filaments ready for spinning.
Today, readily available petroleum white mineral oil is predominantly used, in bulk costing ~US$900/Tonne, whereas vegetable oil eg. appropriate soybean costs ~US$1,550/Tonne.
Batching is made by loading raw jute filaments onto a porous conveyor belt and spraying a mix of oil, water and emulsifier. It is then piled for a specific time to soften filaments before yarn manufacturing.
Percentage oil used varies dependent upon application. As much as 20% mineral oil may be used to retard biodegradation. 5~6% is used for certain CB yarns, but while considered low–JBO content, still smell of kerosene.
Time is also money, and piling may be complete within 48 hours using mineral oil, but can extend to over a week for vegetable oils.
Many vegetable oils can be used, including castor, palm, rice bran. We use high–priced, non–rancidifying 100% Vitamin A/D fortified cold-pressed soybean oil to batch our jute.
Please note, that using vegetable oils does not only make a skinfriendly, non-smelly rope, it also does no harm to the workforce working at the jute mill and the environment surrounding it.
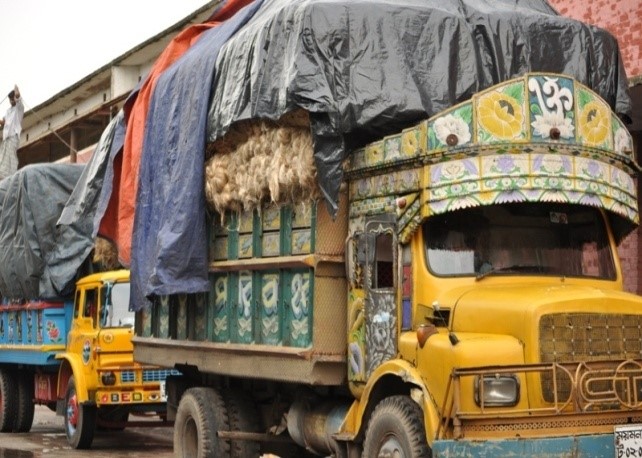
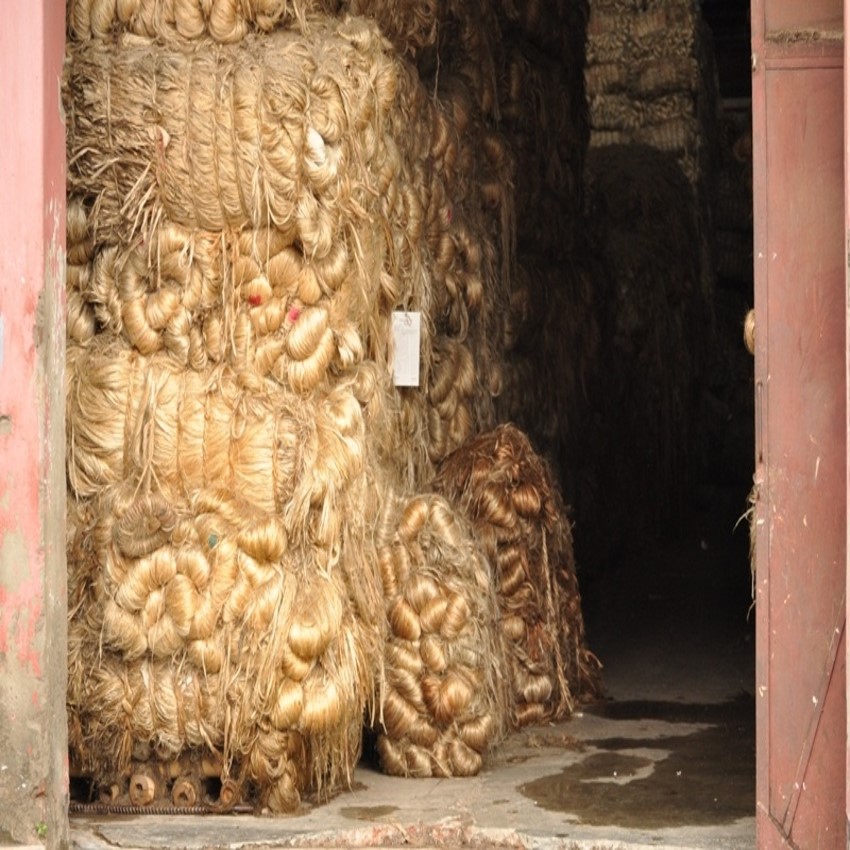
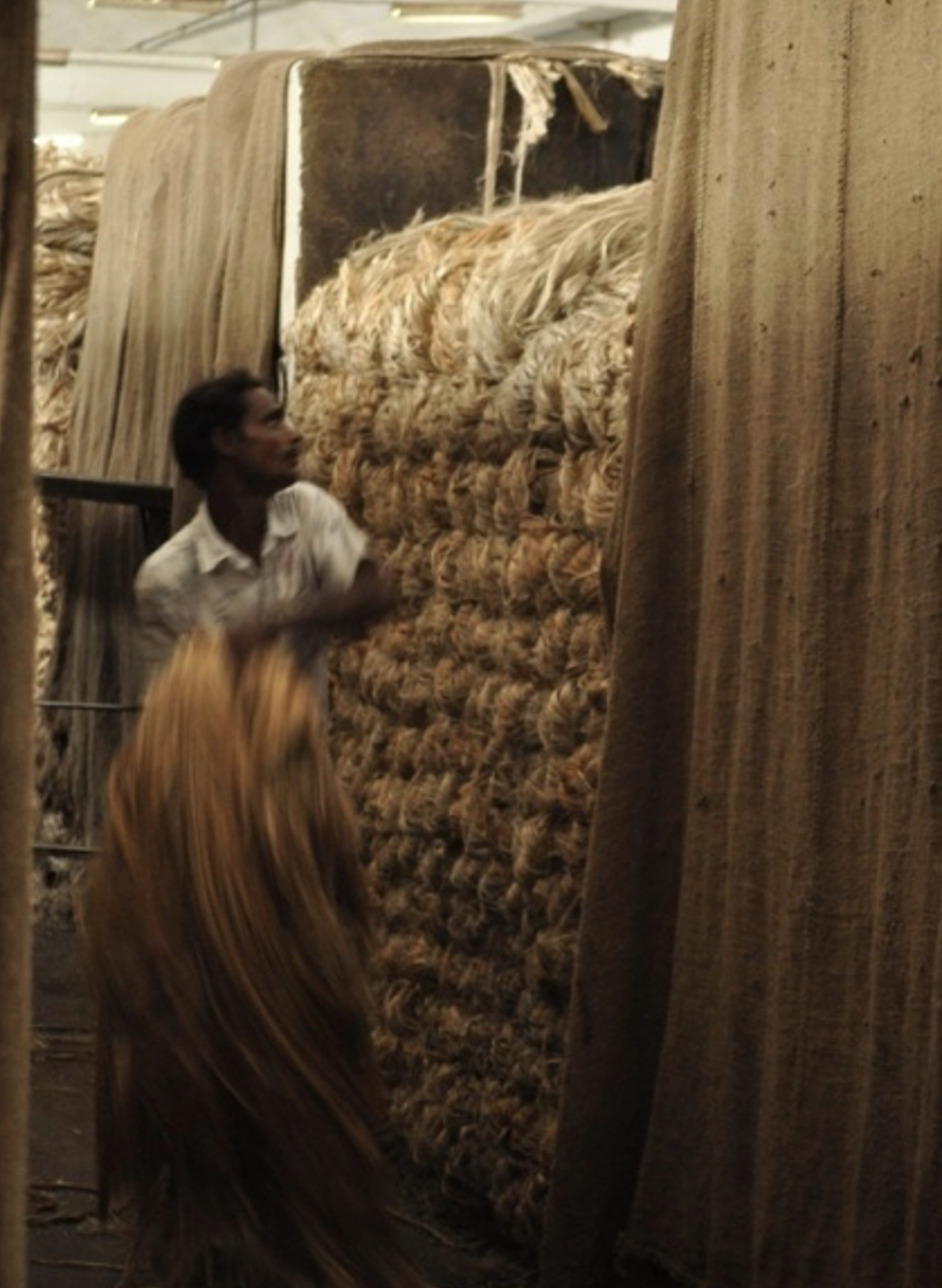
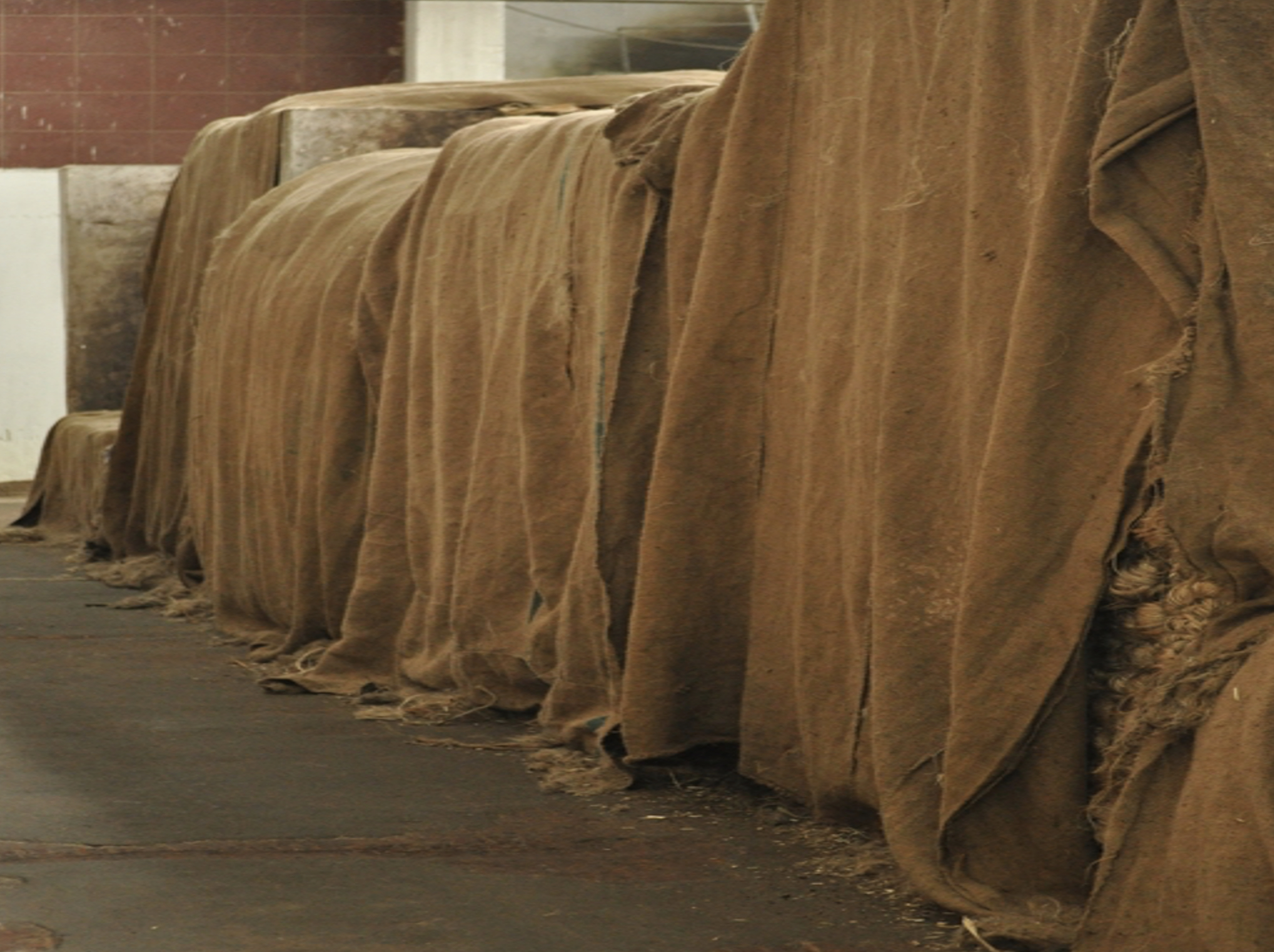
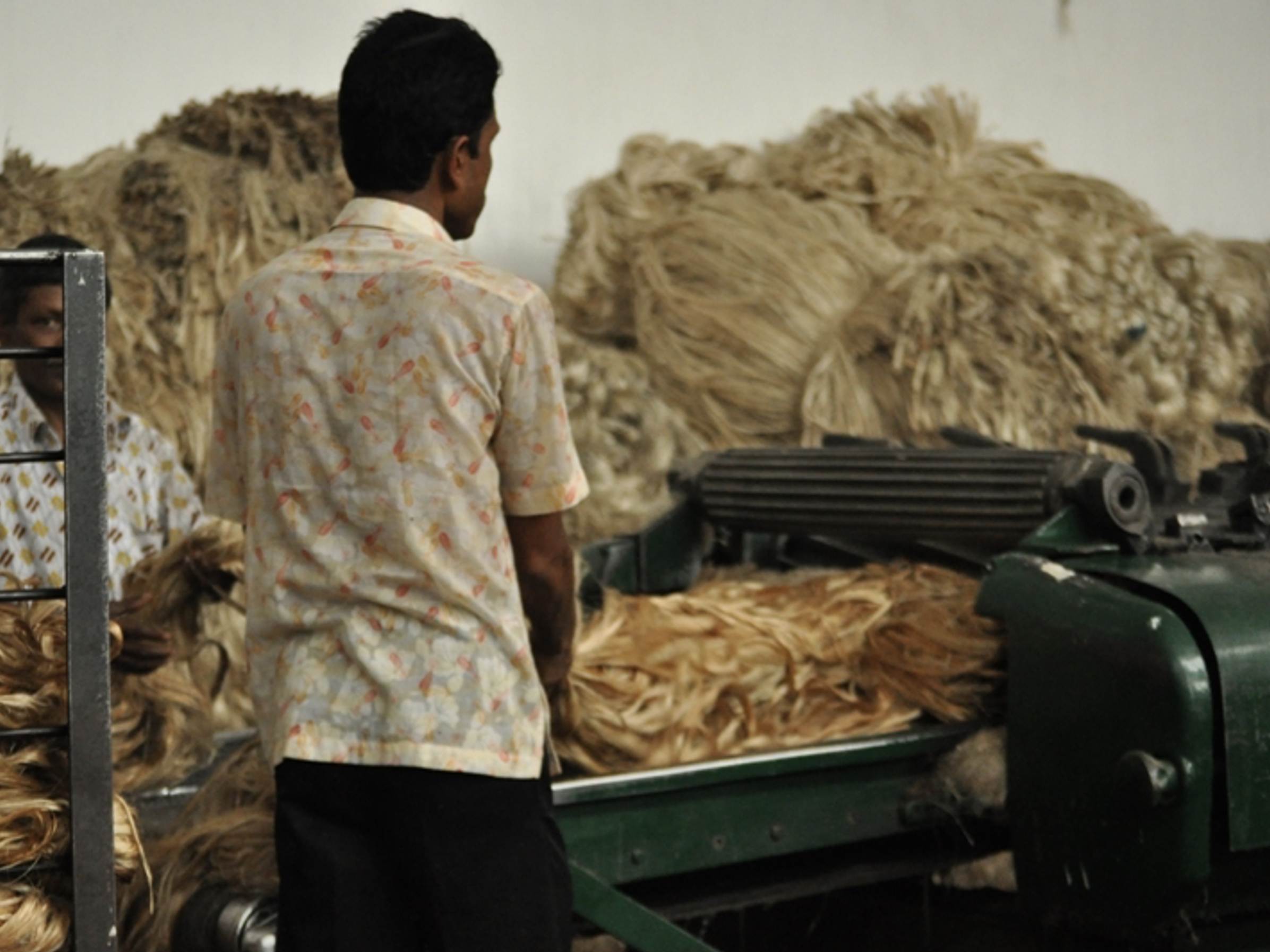